NASA, Blue Origin Support Embry-Riddle Rocket-Testing Partnership with Morgan State University
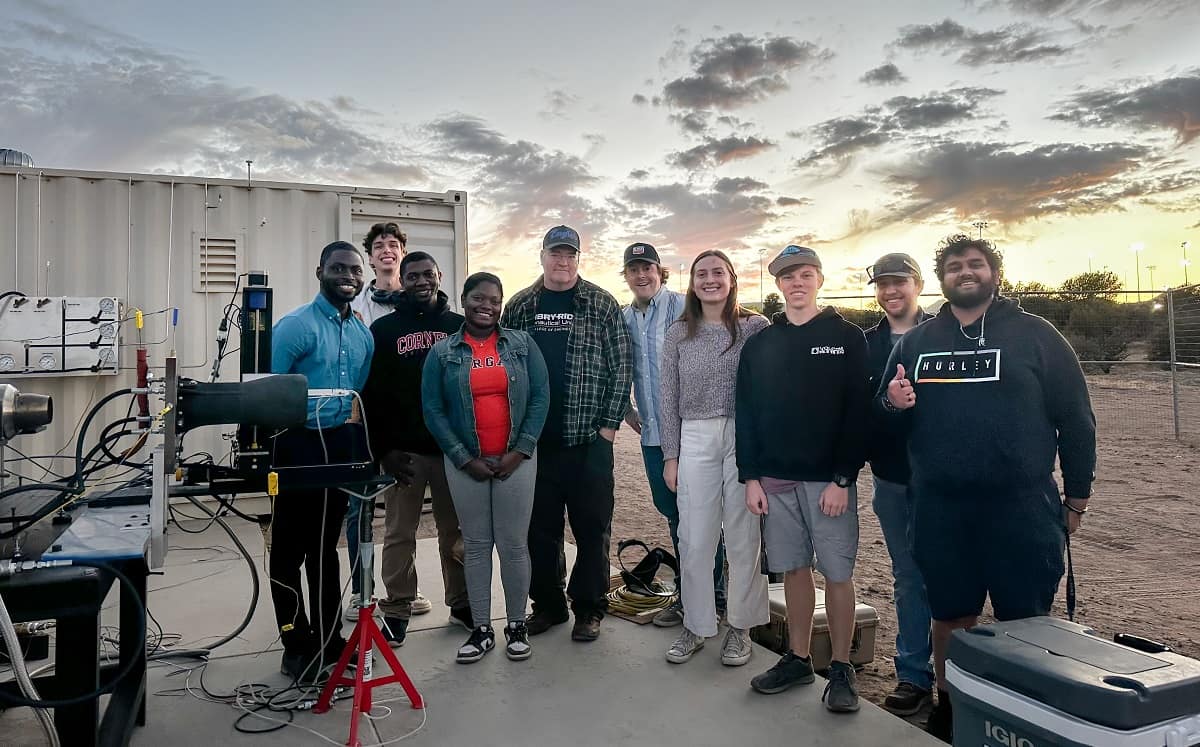
At Embry-Riddle Aeronautical University’s Prescott, Arizona, campus, students this month tested rocket components with their Morgan State University (MSU) peers.
The Rocketry Partnership, supported by NASA Marshall Space Flight Center and Blue Origin, is the latest example of how Embry-Riddle’s Prescott Campus is cultivating the next generation of aerospace leaders and innovators, said Dr. Elliott Bryner, interim department chair and associate professor of Mechanical Engineering in the College of Engineering.
Preparing a robust aerospace workforce is an important goal for Arizona and the country, given the current boom in space enterprise and exploration; the total global space economy, valued at $469 billion in 2021, may grow to $1.1 trillion by 2030, according to a Bank of America Global Research estimate. As a result, the need for new aerospace engineers is expected to increase two times faster than the average for all occupations over the next decade, the U.S. Bureau of Labor has reported.
A Winning Partnership
How did the Rocketry Partnership take shape? Bryner had connected with the project’s principal investigator, Dr. Oluwatobi (“Tobi”) Busari of Morgan State University, through the Propulsion Education Committee of the American Institute of Aeronautics and Astronautics (AIAA). The collaboration seemed like a perfect fit because both Embry-Riddle and Morgan State focus on undergraduate education and hands-on student research.
The Morgan State delegation’s visit to Prescott “is about exposing our students to another rocket facility — one that incorporates all levels of design in an academic context,” said Busari, who is a rocketry research associate with Morgan State’s Clarence M. Mitchell, Jr. School of Engineering. “Working with the students at Embry-Riddle should help both sets of students understand the complexity of the tasks being carried out.”
Last week, the Embry-Riddle and Morgan State students conducted studies of two rocket thrust chambers that were “additively manufactured.” The students “gained important hands-on experience, looking at engine design from its initial inception to a possible full-scale test — the entire life cycle of engine development,” Bryner said.
What Is Additive Manufacturing?
Non-engineers may think of additive manufacturing as “3D printing,” but in fact, the process involves using a laser to fuse a powder copper alloy into solid rocket engine parts, explained Dr. Neil Sullivan, assistant professor of Mechanical Engineering at Embry-Riddle.
Additive manufacturing makes it possible to optimize more integrated designs as well as complex shapes and features, which is why it is an increasingly attractive option for rocket makers.
In March this year, a rocket company called Relativity Space launched what they described as “the first 3D-printed rocket to reach space.” Although the approach is still an emerging technology, Busari said, “The RS25 space shuttle main engine, for example, was recently redesigned with additively manufactured components for the Artemis missions back to the moon.”
Embry-Riddle and Morgan State students investigated how any surface roughness might affect the thermal and hydraulic performance of additively manufactured thrust chambers, or rocket nozzles, Sullivan explained.
Why? In designing rocket thrust chambers, optimizing the heat pickup versus the required pressure drop is key to high performance, Sullivan said. In a common type of commercial rocket — a “regeneratively cooled liquid propellant rocket” — the propellant passes through small cooling passages in the wall of the rocket nozzle before entering the combustion chamber.
Perfecting Rocket Designs
Pushing the propellant through cooling passages requires energy, though, in the form of high-feed system pressure. Too large a pressure drop can reduce propellant flow, which reduces thrust, Bryner noted. If the thrust chamber walls have large roughness created during the additive manufacturing process, the engine will be easier to cool, but it will require higher pressures to achieve optimal performance, Sullivan said.
Busari explained the challenge this way: “The performance of rocket engines can improve significantly if the pressure required to inject the liquids into the engine is reduced. This is a new area of development for additively manufactured rocket engines because surface roughness, which controls this pressure budget, cannot be tailored independent of the geometry of the build. With the data we generate, we can influence some standards that ultimately influence performance limits.”
The students used a gas turbine airplane engine — a PBS Aerospace TJ-40 at Embry-Riddle’s Rocket Test Complex — to generate hot exhaust. In this way, they simulated the hot gases moving through specially fabricated thrust chambers. The rocket engine nominally burns JP-1 (the fuel, which is a refined form of kerosene) and liquid oxygen, which is the oxidizer. The TJ-40 burns Jet-A (a very similar form of kerosene) and air, which generates a very hot exhaust but much cooler than the actual rocket. The students assessed parameters, such as the velocity of the hot gas jet, as well as temperatures and pressures in the cooling jacket to assess its performance.
Embry-Riddle student Gautam Nandakumar noted that Prescott Campus facilities provide unique learning opportunities for undergraduates.
“Instead of just learning about rocketry and propulsion in the classroom, students get the chance to physically build, see and conduct experiments firsthand,” said Nandakumar, a junior pursuing a dual major in Mechanical Engineering with a concentration in Propulsion and Aerospace Engineering focused on Astronautics. “The Rocket Test Complex, in particular, has given students the chance to oversee diverse rocket engine tests, paving the way for a record-breaking flight vehicle and promising even more groundbreaking projects in the future.”
As a career, Nandakumar envisions “playing a pivotal role in a leading rocket company, focusing specifically on the design and management of rocket nozzles and injectors.” He also has a keen interest in propulsion. “Taking the foundational knowledge and experience I’ve garnered at Embry-Riddle and applying it to meet and elevate industry standards is the dream I strive for,” he said.
Already, Nandakumar is well on his way, having completed an internship with Collins Aerospace.
Busari expressed appreciation for Morgan State’s collaboration with Embry-Riddle at Prescott. “The welcoming spirit of our collaborators has made the partnership easy, and we are very grateful,” he said.