To Err is Human: Improving Workplace Safety Through Experience
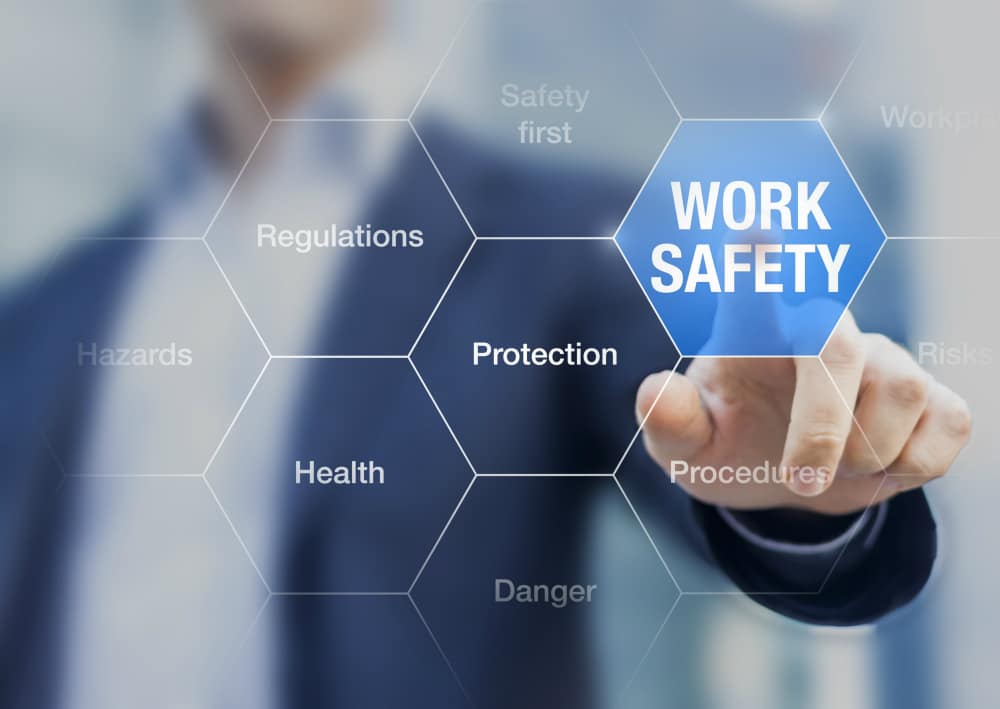
It is well known that human error accounts for vast majority of accidents, injuries and quality defects. While the impact varies, the data gathered as a result provide valuable insights for improvements.
“It’s disappointing that people talk about human error as if those who commit errors are somehow bad,” said Dr. Scott Shappell, professor of human factors and systems at Embry-Riddle Aeronautical University. “Human error is a natural phenomenon. At what point in our lifecycle did we flip a switch and suddenly have to be 100% accurate, all the time? By definition, humans make mistakes. The key is recognizing when we make those mistakes and either preventing them and/or mitigating their consequences.”
Mistakes are not typically made because people don’t care; there is usually much more involved. However, it’s critical to figure out what caused the error.
“As a business, in any industry, it’s great to have a goal for a zero percent accident rate, but the reality is people will always make mistakes,” said Shappell. “We aren’t accepting the mistakes, but rather looking to recognize how they were made. In other words, what was different that day than any other day?”
That’s where the Human Factors Analysis Classification System (HFACS) comes in. Recognized as the gold standard in human factors analysis and classification, HFACS applies to accident investigation and analysis, risk reduction and safety, quality and productivity improvement efforts.
“HFACS forces you to look beyond the individual who made the mistake and ask yourself tough questions, including whether the supervisor or the organization played a role in these errors,” shared Shappell.
At the Unsafe Act level, the system identifies three types of errors (i.e., skill-based, decision, and perceptual errors) and two types of violations (i.e., routine and exceptional violations).
“The way we resolve these unsafe acts are very different depending on the type of error and/or violation committed,” explained Shappell. “HFACS works to identify and address specifically how to fix issues associated with each.”
Accident and incident investigations tend to center around preventing a problem from happening again. To do this, you must understand the entire problem – not just the symptoms.
“The standard mindset in accident investigations is that someone has to pay,” said Shappell. “I’ve read a number of accident investigations, all of which focus on the same four types of interventions: a policy or procedure, training, automation that writes the human out of the system and some form of punishment or accountability. That’s not necessarily the solution. The Human Factors Intervention Matrix (HFIX) helps people identify novel solutions beyond what we might normally come up with.”
The Embry-Riddle HFACS professional education course is an in-depth opportunity for participants to learn how to think outside of the box when looking at human errors and preventing them.
“We provide hands-on tools that look beyond standard intervention tactics through this course,” said Shappell. “It’s all interactive and we cover how to investigate errors, classify archival data, and develop interventions for dealing with errors.”
This course is a partnership between Embry-Riddle and HFACS, Inc., which has trained more than 8,000 students over the past 15 years.
“We’ve directly trained more than 200 industries, including major air carriers, health care, mining and even Disney,” said Shappell, who is also a member of the HFACS team. “This partnership is really important because it allows us to provide CMEs and CEUs, as well as professional human factors certificates.”
The next two-day training workshops take place May 7-8 in Daytona Beach, Florida, and July 16-17 in Las Vegas, Nevada. For more information, visit https://proed.erau.edu/courses/hfacs.