Keeping Gas Turbines Healthy
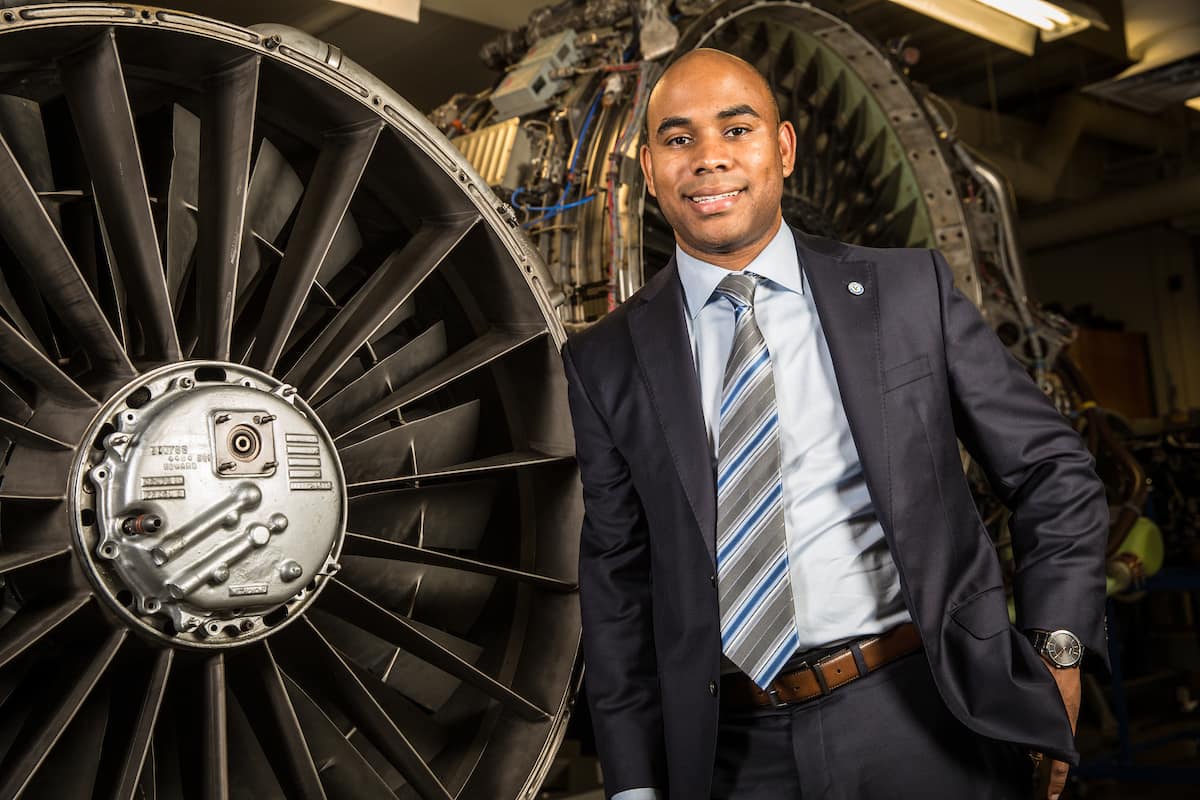
Inside big ships, jets, rockets, hospitals, factories, oil-drilling rigs and many other operations, a type of internal combustion engine called a gas turbine reliably generates power. But routine maintenance comes with a steep price tag. Over a typical 10-year life span, keeping a gas turbine healthy may run as much as $30 million, says Reamonn Soto, whose startup business, Sensatek Propulsion Technology, offers a way to reduce those costs significantly while also increasing the efficiency of power generation.
Soto, a U.S. Marine Corps veteran who is pursuing a master’s degree in aeronautics at Embry-Riddle Aeronautical University’s Worldwide Campus, has been piling up competitive awards for his business model. In addition to a $25,000 seed grant from the nonprofit FireSpring Fund, Soto has won: $10,000 and first place in this year’s Launch Your Venture competition; the $50,000 grand prize in the U.S. Department of Energy’s 2016 Megawatt Ventures contest; a $50,000 business travel budget from the National Science Foundation’s Innovation Corps (iCore) program and more.
The Secret to the Sensors’ Success
From a technical perspective, all the fuss is warranted, says Mark Ricklick, an Embry-Riddle assistant professor of aerospace engineering who serves as an advisor to Soto’s company. Sensatek licenses patented technology to manufacture ceramic sensors that precisely and wirelessly measure gas turbine temperatures. This allows operators to prevent failures and optimize engine performance by modifying temperatures, as needed.
Sensatek has positioned itself to address a critical business need. The efficiency of a gas turbine improves when combustion temperatures are higher – 500 to 800 degrees Celsius, above the safe operating temperatures for materials, Ricklick explains. Dialing down the heat too suddenly can also cause failures. To optimize performance without breaking anything, operators have to take the engine’s temperature on a continuous basis. Yet, currently available sensors cannot be placed near the engine’s hottest spot – the turbine inlet – so temperature readings are captured in cooler locations. Mathematical models are then used to estimate heat levels.
Soto’s company is commercializing a different type of sensor, originally developed at the University of Central Florida, based on a polymer-derived ceramic material that is easy to fabricate and tolerates high temperatures well. The sensors can also be “tuned” with doping agents to send different frequency signals to a remotely located antenna. “The resonant frequency of these sensors changes in response to temperature,” Ricklick explains. “They act as little passive antennas. The frequency of the sensors can be manipulated to correspond with a particular temperature.”
Even with a 1 percent improvement in gas turbine efficiency, Soto says, operators could save $480,000 per engine every year. Optimizing performance can also extend the life of a gas turbine, he notes.
The Sensatek research team is currently investigating how to position the sensors on engines to get the best results for customers. Meanwhile, Soto continues to soldier on -- networking, learning as much as he can about the technology and refining his business model based on customer feedback.
“We’ve been like a quiet storm for the past two years,” he says. “We’ve been going out there, attending industry conferences, cold-calling business leaders and showing up where it’s least expected to get the answers we need. We want to better understand how our research can have a positive impact on society and real economic consequences as well.”
Editor’s Note: This article was originally published in the Fall 2017 edition of ResearchER magazine (Vol. 1, No. 2). The ResearchER archives can be found on Scholarly Commons.