Embry-Riddle Aviation Safety Expert Unites Industry to Safeguard Aviation Supply Chain
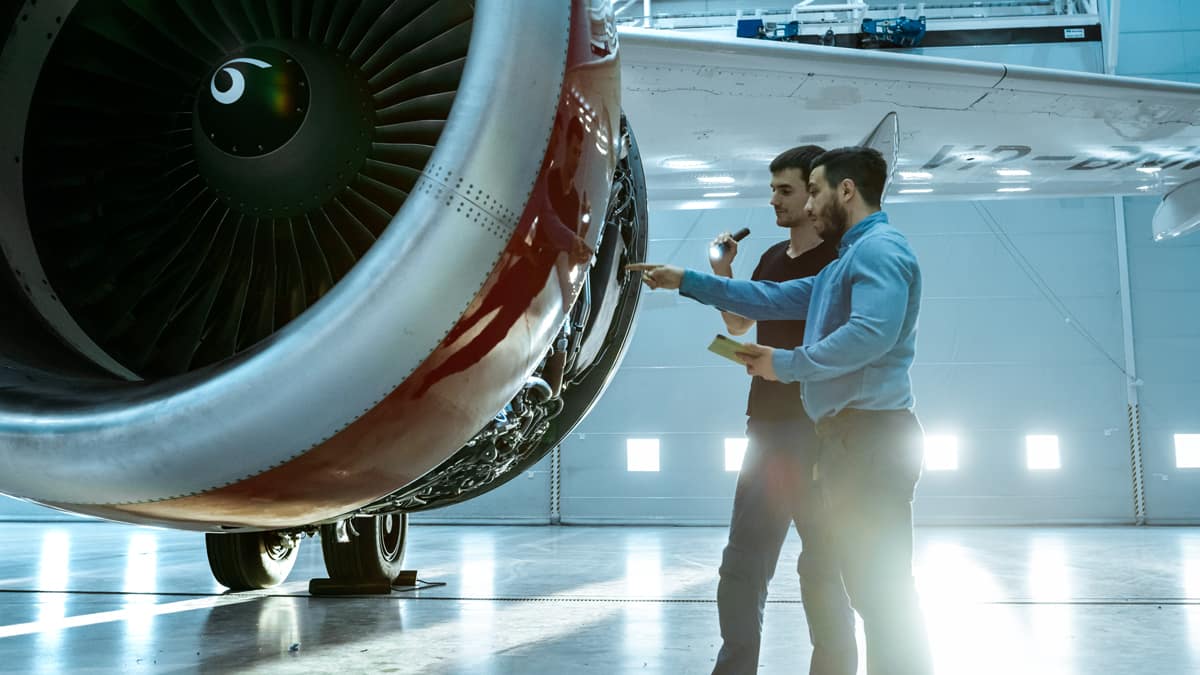
In the summer of 2023, a receiving clerk in the procurement department of TAP Air Portugal, a Lisbon-based airline, made a curious discovery: A $65 engine part that should have appeared brand-new showed signs of significant wear. The clerk checked the documentation from the London-based parts supplier and noticed that the submitted documentation was also suspicious.
Using his safety training, the employee immediately reported the anomaly to TAP Air Portugal management, which raised the issue with the jet engine’s manufacturer. Little did the procurement clerk know at the time, but this escalation led to one of the biggest investigations in the history of the aviation supply chain, as reported by Reuters and the British Broadcasting Corporation late last year.
The discovery also marshaled an immediate response from regulators worldwide. Nearly all major airlines were affected when they were forced to temporarily ground aircraft on which the spare parts in question had been installed. Though the number of engines impacted was relatively small compared to the size of the global fleet, the incident underscored the need for additional safeguards in the Maintenance, Repair and Overhaul (MRO) industry.
According to the Honorable Robert L. Sumwalt, executive director for the Boeing Center for Aviation & Aerospace Safety at Embry-Riddle Aeronautical University and former National Transportation Safety Board (NTSB) chairman, “The vast majority of MRO companies were doing the right thing and acting with a safety and regulatory mindset, but this situation certainly begged the question—what can we do to be even safer?”
Formation of Coalition to Enhance Safety
In February 2024, an independent Aviation Supply Chain Integrity Coalition was formed. Sumwalt and former United States Transportation Deputy Secretary, the Honorable John D. Porcari, were tapped as the group’s co-chairs.
The overarching goal of the coalition, which included a wide range of companies from across the aerospace and aviation sectors, was to recommend actions to prevent unapproved propulsion parts from entering the supply chain and to bolster the overall integrity and safety of the aviation supply chain.
“Through this coalition, we worked to find lasting solutions that the industry can adopt to improve the overall integrity of the aviation supply chain,” Porcari said.
The group interviewed more than 38 experts from 24 organizations outside the coalition. Those consulted included industry associations, parts brokers, airlines, MRO shops and aircraft and engine manufacturers. The coalition also visited one of the world’s largest MRO shops to see firsthand the challenges and opportunities represented by various potential solutions.
The Honorable Robert L. Sumwalt and the Honorable John D. Porcari visit a Maintenance, Repair and Overhaul (MRO) shop as part of their work as co-chairs of the Aviation Supply Chain Integrity Coalition. (Photo: Matthew Lehner/GE Aerospace)
Actionable Recommendations
Ultimately, the coalition offered 13 comprehensive recommended actions in the group’s final report, which was issued on Oct. 9. The actions are grouped into three categories: vendor accreditation; document traceability and verification; and non-serialized parts traceability. Each category includes associated actions to be implemented in the short term (12-24 months), medium term (within the next 5 years), and long term (over 5 years).
According to Sumwalt, short-term actions can be put into effect immediately, or in a matter of weeks or months. The medium- and long-term actions will require more effort on the part of MROs and suppliers. “This is an excellent start, but it’s important that we don’t take our eye off the ball,” he said.
Bolstering Aviation Supply Chain Safety
As a result of this incident and the ensuing investigation and safety recommendations, the aviation supply chain has been strengthened. However, a sustained supply chain safety culture for MRO companies and the aviation industry will take time to mature.
Several companies have already started to implement some of the recommended actions, but many companies throughout the aerospace ecosystem will need to take action to have the most significant impact.
“We are asking coalition companies, along with industry associations, governmental organizations, and educational institutions, among others, to share the coalition’s report broadly across the industry to determine which actions can be implemented to strengthen the overall integrity of the aviation supply chain,” Sumwalt said.
Together, he added, the industry can mitigate current risk and anticipate future challenges, ensuring the continued safety and trust of the global aviation community.