Advanced Manufacturing Technology Powers Embry-Riddle Research, Readies Eagles for High-Tech Careers
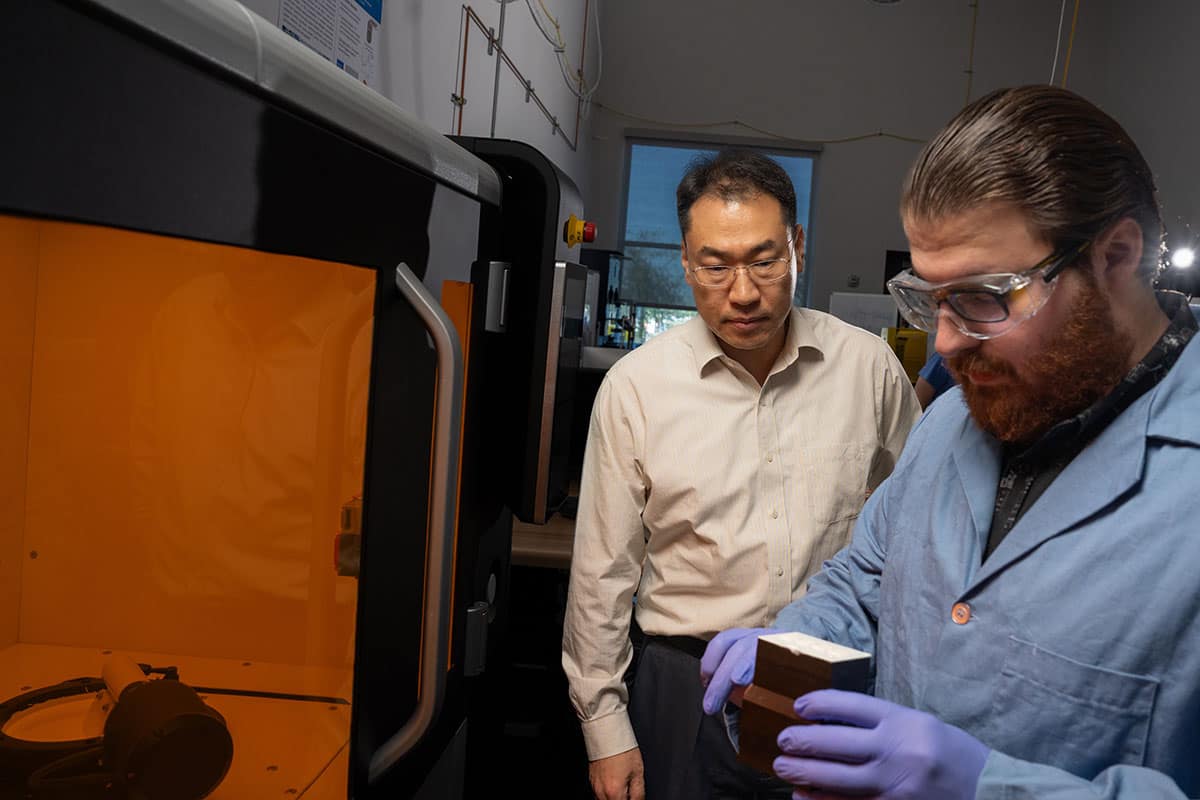
When sophomore Avi Waghray heads into the work world of aerospace engineering, he feels confident that his experience with state-of-the-art manufacturing equipment at Embry-Riddle Aeronautical University will make him stand out among job candidates.
Using a newly acquired 3D ceramic printer at Embry-Riddle, Waghray has worked on producing a bio-inspired ceramic coating material for a lunar lander to reduce damaging moondust adhesion. The ultra-durable material is modeled after lotus leaves, whose surface pattern makes them self-cleaning and impervious to water.
“I definitely think having hands-on experience with high-level equipment has given me an edge in the job search,” said Waghray.
Embry-Riddle has recently expanded its research capabilities in a wide range of fields through a $5 million investment in advanced manufacturing equipment. The new equipment, whose purchase was financed by the Florida Department of Education, will be used in areas that include hypersonics, space and energy, “where some of the biggest challenges can be addressed with new and improved materials systems that advanced manufacturing can help create and scale,” said Dr. Seetha Raghavan, professor of Aerospace Engineering.
The printer used by Waghray, called the Lithoz CeraFab Multi 2M30, is the first of its kind to be installed in the United States. It produces material by a layering process called additive manufacturing and is capable of creating patterns the size of a micron, or a millionth of a meter, layering different kinds of ceramics as well as ceramic and metal.
“Additive manufacturing with such high precision is extremely novel and definitely something that will shape the future of aerospace,” Waghray said.
Ashley Tirado Pujols, who is concentrating on the structure of materials in her master’s program, said using Embry-Riddle’s advanced equipment in her work as a NASA Space Technology Graduate Research Fellow has been extremely valuable to her development.
“We undergo a lot of training to properly use all of our equipment, which allows us to become more creative in the way that we are manufacturing our materials,” she said. “It's truly helped in pushing our creativity, our skills and our communication.”
In addition to the Lithoz printer, the new equipment includes a spark plasma sintering system called the SUGA-2000 that provides rapid densification of metals, ceramics and composites with high pressure and electric current. It will help researchers working on the materials used in high-temperature or other extreme-environment applications, including hypersonics and space.
A new atomic-layer deposition system performs nanofabrication for applications such as electronics and advanced sensors, and the OrbitalS large-scale automated composite manufacturing system can produce next-generation aerospace, automotive and composite structures. Finally, a new Bruker AFM materials testing system will help researchers evaluate the quality of the advanced materials manufactured by these systems.
“With these capabilities, the university now supports research spanning the nanoscale to large structural components, covering metals, ceramics, polymers and hybrid materials,” said Raghavan. “This investment strengthens interdisciplinary collaboration and accelerates innovation, reinforcing the university’s position as a leader in advanced manufacturing research. We anticipate this will drive discoveries, enhance industry partnerships and train the next generation of engineers and scientists, ensuring Embry-Riddle remains at the cutting edge of materials and manufacturing technology.”
Dr. Jeremy Ernst, Embry-Riddle’s vice president for research and doctoral programs, said the new equipment will accelerate the pace of research and, at the same time, familiarize students with the latest tools and techniques needed in today’s workplace.
“Enhanced capabilities, supported by state-of-the-art research equipment, drive discovery and innovation,” Ernst said. “Leading researchers with access to these advanced tools are further enabled to investigate new materials, processes and phenomena. These types of investigations also meaningfully contribute to cutting-edge student research experiences, shaping future opportunities and prospects.”